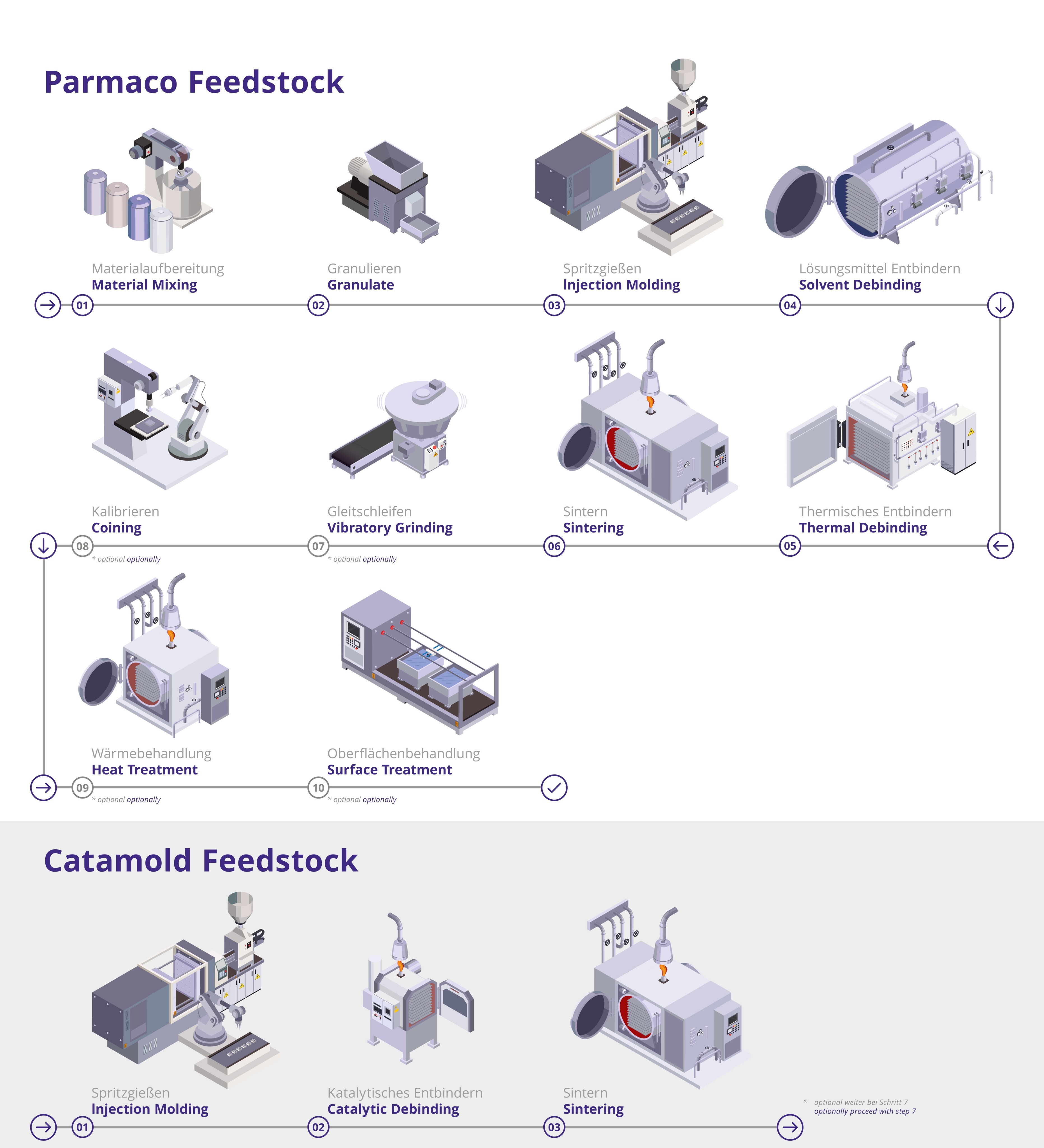
MIM (Metal Injection Molding) ist ein innovatives Formgebungsverfahren für die Herstellung von hochfesten, komplex geformten metallischen Klein- und Kleinstteilen.
Werkzeuge mit MIM gerechtem Teiledesign
Wesentliche Voraussetzung für zeichnungskonforme MIM-Teile ist ein präzises Spritzgiess-Werkzeug, das eine hohe Verschleissbeständigkeit gegenüber der abrasiven Wirkung des MIM-Pulvergemischs (Feedstock) aufweist.
Das MIM-Verfahren kombiniert zwei bekannte Fertigungstechnologien:
1. Kunststoff-Spritzgiessen
Diese seit vielen Jahrzehnten bekannte und bewährte Technologie ermöglicht die Herstellung
komplex geformter Teile aus Kunststoff. Dank der Verwendung von
Werkzeugen mit Schiebern können auch Teile mit Hinterschneidungen
erzeugt werden. Beim Spritzgiessprozess wird Kunststoffgranulat in
einem speziellen Aggregat aufgeschmolzen und dann in flüssigem Zustand
unter hohem Druck in eine Stahlform gespritzt. Nach der Erstarrung kann
das Fertigteil entnommen werden. Das Spritzgiessen hat die Formgebung im
Kunststoffbereich revolutioniert und ist heute aus der
industriellen Fertigung nicht mehr wegzudenken.
2. Sintern von Metallpulver-Presslingen (P/M Verfahren, Pressintern)
Auch diese Technologie wird schon seit Jahrzehnten angewendet, um aus
Metallpulvern verschiedenster Legierungen, hochfeste Metallteile
herzustellen. In einem ersten Schritt wird hierbei Metallpulver mit
grosser Kraft in eine Form gepresst, wodurch man einen "grünen"
Pressling mit noch geringer Festigkeit erhält. Dieser wird einer
Hochtemperatur-Wärmebehandlung (Sintern) unterzogen, in deren Verlauf die
Metallpartikel durch Diffusionsprozesse zusammenwachsen. Dadurch bildet
sich ein stabiles metallisches Teil, dass der Form des Presswerkzeugs
entspricht. P/M ist ein wirtschaftliches Verfahren zur Herstellung von
einfach geformten Metallteilen.
Metal Injection Molding vereint beide Technologien
Als erstes wird aus sehr feinen Metallpulvern und Kunststoff eine spritzfähige
pastöse Masse hergestellt, welche einen Metallpulvergehalt von über 90
Gewichts-% aufweist. Dieses Material wird mit einer konventionellen
Spritzgiessmaschine, ganz wie auch beim Kunststoffspritzgiessen, zu
Formteilen verarbeitet. Anschliessend wird der Kunststoffanteil, der die
Formgebung erst ermöglicht hat, aus den Formteilen herausgelöst, ohne
dass die Teile dabei ihre Form verlieren. In einem weiteren Schritt
werden sie gesintert und erhalten so die gewünschten Eigenschaften,
insbesondere eine hohe Festigkeit.
Vorteile des MIM-Verfahrens
Hervorragende Formgebungsmöglichkeiten
Mit dem MIM-Verfahren können selbst sehr komplex geformte Teile ohne oder mit nur wenig Nacharbeit
hergestellt werden. Hinterschneidungen, die mit dem konventionellen
P/M-Sinterverfahren nicht darstellbar sind, lassen sich mit MIM
problemlos realisieren. Ein besonderer Vorteil der von Parmaco
perfektionierten Variante des Verfahrens ist die hervorragende Abbildung
selbst feinster Werkzeugkonturen, da das extrem fliessfähige Material
die exakte Ausformung sehr scharfer Ecken und Kanten erlaubt.
Sehr gute Materialeigenschaften
Im Gegensatz zum konventionellen Pressen und Sintern, wo üblicherweise
Dichten von 90 % der theoretischen Werkstoffdichte erzielt werden,
erreichen MIM-Bauteile Dichten zwischen 96 % und 100 %. Dadurch werden
Materialeigenschaften erreicht, die weitgehend jenen von Teilen
entsprechen, die durch Zerspanung aus dem Vollen gefertigt wurden. Eine
herausragende Besonderheit des MIM-Verfahrens ist die Möglichkeit, durch
passende Pulvergemische "unmögliche" Legierungen zu erzeugen, die
mit metallurgischen Schmelzverfahren gar nicht oder nur mit
unverhältnismässig hohen Kosten hergestellt werden können. Dazu gehören
beispielsweise auch Legierungen mit exakt definiertem thermischem
Ausdehnungskoeffizienten.
Hervorragende Oberflächenqualität
Die Oberfläche von MIM-Teilen ist jener von Feingussteilen weit
überlegen. Selbst ohne eine Polierbehandlung wird eine Rautiefe von Ra
< 1.2 erreicht. Dadurch lassen sich Bearbeitungs- und
Polierkosten eliminieren oder erheblich reduzieren.
Enge Toleranzgrenzen
Das MIM-Verfahren ermöglicht es, ohne Nachbearbeitung eine Genauigkeit besser
als ± 0,3 % des Sollmasses einzuhalten. Dies bedeutet, dass bei
Kleinstteilen die Genauigkeit im Bereich von Hundertstel mm
liegt. Bei sehr eng tolerierten Teilen oder bei Teilen mit
grösseren Abmessungen (grösser als ca. 30 mm) kann eine
Kalibrierung oder Nachbearbeitung erforderlich werden.
Werkstoffpalette
Da MIM-Teile in der Regel nicht mechanisch nachbearbeitet werden müssen, bietet das MIM-Verfahren um so grössere Vorteile, je schwieriger ein Material bearbeitbar ist. Dies gilt insbesondere für rostfreie Stähle, weichmagnetische Legierungen, Eisen/Nickel-Werkstoffe, aber auch Werkzeugstähle und Sonderlegierungen.
Alle Härteverfahren können bei MIM-Teilen ebenfalls, wie beim vergleichbarem Vollmaterial, ohne weiteres angewandt werden. Auch alle Oberflächenbehandlungsverfahren wie z.B. Vernickeln, Hartverchromen etc. lassen sich anwenden.
Wirtschaftlichkeit
Die Wirtschaftlichkeit des MIM-Verfahrens hängt in hohem Masse davon ab, wie gut die erzielbaren Werkstoffeigenschaften und die gestalterischen Möglichkeiten des Verfahrens zum geplanten Einsatzzweck passen. Obwohl die Kosten des Verfahrens vergleichsweise hoch angesiedelt sind, ermöglicht es im Vergleich mit alternativen Prozessketten enorme Einsparungen. Ob sich sein Einsatz für eine bestimmte Anwendung lohnt, wird daher von Fall zu Fall geprüft. Dabei ist es von grösster Bedeutung, dass sich der Konstrukteur über die Möglichkeiten des MIM-Verfahrens im Klaren ist.
Ein für das
Stanzverfahren konstruiertes Teil dürfte bei einer 1:1 Herstellung im
MIM-Verfahren immer teurer sein. Werden jedoch die Möglichkeiten
des MIM-Verfahrens bereits beim Konstruieren berücksichtigt, so können
hierdurch oft Funktionen ins Teil integriert werden, die erhebliche
Vereinfachungen der ganzen Baugruppe erlauben. Oft ist es möglich,
die Anzahl der erforderlichen Teile zu reduzieren, Bearbeitungskosten
im Vergleich zu konventionell hergestellten Teilen zu eliminieren oder
durch geeignete Materialwahl die Qualität des Bauteils zu erhöhen.
All dies kann zu erheblichen Vorteilen bei Kosten und, oder
Gewicht führen.
Auf die Wirtschaftlichkeit des MIM-Verfahrens wirken sich positiv aus
- nahezu unbegrenzte Formgebungsmöglichkeiten
- enge Fertigungstoleranzen
- gute mechanische Eigenschaften
- hohe Oberflächengüte
- spezielle Legierungsanforderungen
Das MIM-Verfahren ist dort am wirtschaftlichsten, wo komplex geformte Klein- und Kleinstteile mit engen Toleranzgrenzen, guten mechanischen Eigenschaften und hoher Oberflächengüte verlangt werden.
Wenn z.B. bei Teilen, welche bei Herstellung im Feingiessverfahren nachträglich noch bearbeitet werden muss, bei alternativer Realisierung mithilfe des MIM-Verfahrens eine Nachbearbeitung entfallen kann, so hat dies häufig einen erheblichen Wirtschaftlichkeitsvorteil zugunsten der MIM-Teile zur Folge. Dies gilt insbesondere dann, wenn die Teile eher klein sind (< 20 g), weil kleine Teiledimensionen in der Regel die Bearbeitung erschweren und damit verteuern.
Wenn das konventionelle P/M Verfahren wegen der Komplexität des Teils oder wegen der Materialeigenschaften nicht in Frage kommt, bietet sich das MIM-Verfahren als Lösung an.
Wenn einer mechanischen Bearbeitung Grenzen gesetzt sind, z.B. durch den Werkstoff, eine ungünstige Geometrie oder unzureichende Spannmöglichkeiten, dann stehen vor allem die Formgebungsmöglichkeiten des MIM-Verfahrens im Vordergrund.
Das MIM-Verfahren eröffnet dem Konstrukteur neue gestalterische Freiheitsgrade. Gerade wegen seiner einzigartigen Möglichkeiten kann es dort eingesetzt werden, wo andere Verfahren aus Kosten- oder Qualitätsgründen an Grenzen stossen oder wo die Teile mit anderen Verfahren schlicht nicht herstellbar sind.
Nachteilige Auswirkungen auf die Wirtschaftlichkeit des MIM-Verfahrens haben die vergleichsweise hohe Kosten
beim Materialbeim Fertigungsprozesses-
und beim Werkzeug
Je schwerer und grösser beispielsweise ein Teil ist, desto mehr fällt der Materialpreis und die Prozesskosten im Vergleich mit anderen Kostenbestandteilen ins Gewicht. Beim MIM-Verfahren kommen sehr feine Metallpulver zum Einsatz, die einen entsprechend hohen Preis haben. Der entsprechende Kostennachteil veringert sich umso mehr, je kleiner und leichter das Bauteil ist. Deshalb kommt das MIM-Verfahren bevorzugt bei Klein- und Kleinstteilen zum Einsatz. Der Nachteil der hohen Materialkosten wird andererseits dadurch entschärft, dass beim MIM-Verfahren das Material zu 100 % ausgenutzt werden kann. Selbst Reste des Spitzgiessprozesses lassen sich wiederverwerten, so dass praktisch keine Materialverluste auftreten. Üblicherweise liegt die obere Grenze des Teilegewichts bei ca. 70 g, die untere dagegen bei ca. 0,01 g.
Die Kosten der weiteren Stationen des Fertigungsprozesses wirken sich ebenfalls stark auf die Kosten der MIM-Teile aus. Je grösser die Teile sind, desto weniger davon passen in die Öfen. Ähnlich wie beim Teilegewicht bedeutet dies, dass die Kosten pro Teil umso mehr sinken, je kleiner sie sind. Die obere Grenze der Teileabmessungen liegt üblicherweise bei ca. 70 mm. Kleinstteile mit Abmessungen im Bereich von 0 bis 15 mm eignen sich jedoch grundsätzlich noch besser.
Ganz wie auch bei Kunststoffspritzgiess-Werkzeugen führen die relativ hohen Werkzeugkosten bei
MIM dazu, dass für Ihre Amortisation eine gewisse Minimalmenge
gefertigt werden muss. Die Definition einer exakten Minimalstückzahl ist
jedoch erst nach genauer Prüfug des Einzelfalls möglich, da die
Wirtschaftlichkeit von den Kosten der gesamten Prozesskette und nicht
allein von den reinen Werkzeugkosten bestimmt wird. Als Daumenregel kann
man von einer Mindeststückzahl von etwa 10'000 pro Jahr ausgehen.
Dieser Wert kann jedoch fallweise auch teils deutlich unterschritten
werden.
Konstruktionshinweise
Weil das MIM-Verfahren dem Konstrukteur wichtige neue
Freiheitsgrade ermöglicht, ist es von grosser Bedeutung, diesen Umstand
bereits im Anfangsstadium der Entwicklung mit in die Überlegungen
einzubeziehen. Je konsequenter ein Teil für das MIM-Verfahren entwickelt
wird, desto grösser können die funktionellen und wirtschaftlichen
Vorteile beim Endprodukt sein.
Bei der Konstruktion von MIM-Teilen gelten grundsätzlich die gleichen Richtlinien wie bei Kunststoff-Spritzgussteilen. So können sich massive Querschnitte auch beim MIM-Verfahren nachteilig auf die Massgenauigkeit auswirken. Auch sollten die Teile so konstruiert werden, dass sie erforderlichenfalls mit Schiebern entformbar sind. Dabei sollte beachtet werden, dass die Kosten des Formwerkzeugs mit jedem zusätzlichen Schieber ansteigen. Parmaco ist gerne bereit, seine Kunden schon im Anfangsstadium von Neuentwicklungen bezüglich des MIM-Verfahrens zu beraten und seine Kenntnisse und Empfehlungen in den Entwicklungsprozess seiner Kunden als Entwcklungspartner einzubringen.